Introduction
In modern industrial environments, sensor plays a crucial role in ensuring safety and efficiency. These devices monitor various parameters, provide real-time data, and enable automated responses to potential hazards and inefficiencies. The integration of sensors in industrial processes leads to significant improvements in operational performance and worker safety.
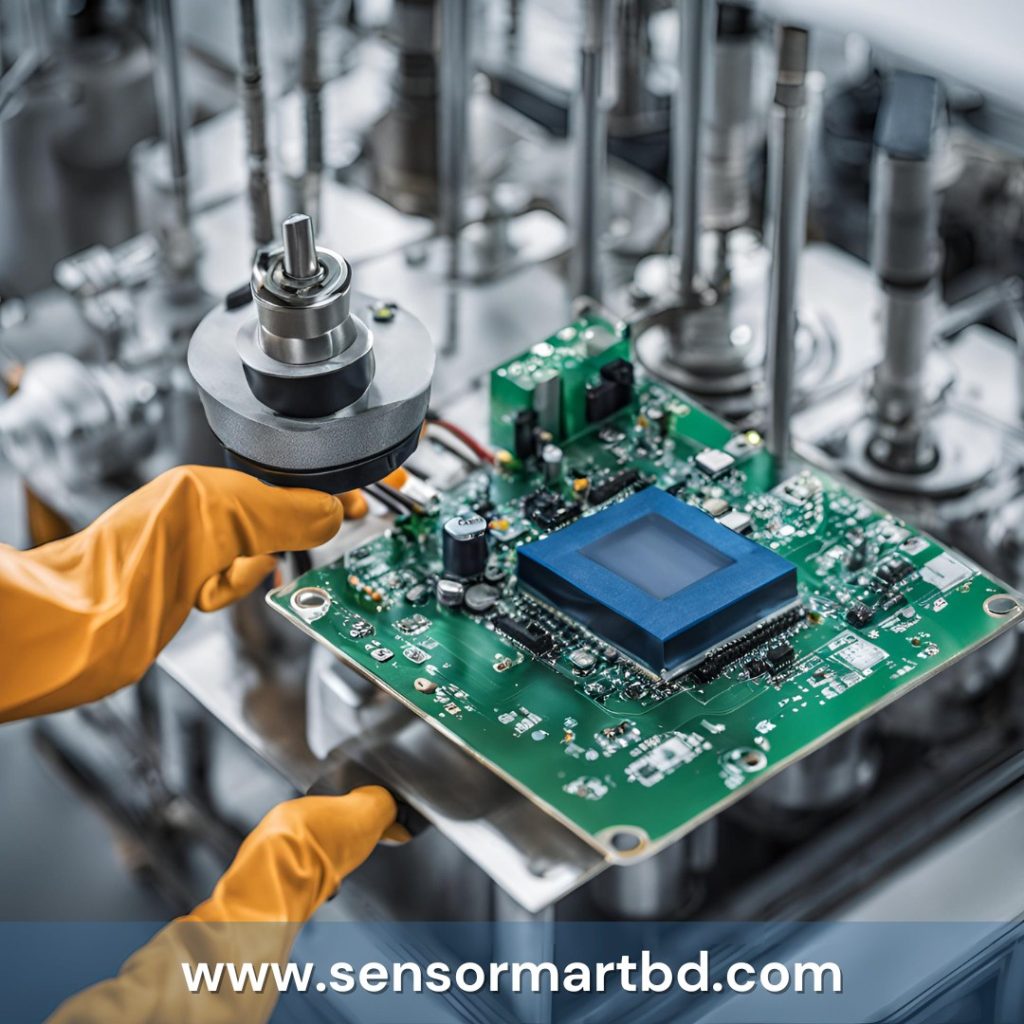
Types of Sensors and Their Applications
- Temperature Sensor:
- Application: Monitor and control the temperature of machinery and environments to prevent overheating and ensure optimal operating conditions.
- Impact: Prevent equipment failure, reduce energy consumption, and enhance product quality.
- Proximity Sensor:
- Application: Detect the presence or absence of objects within a specified range, often used in machinery and robotics.
- Impact: Improve automation, reduce human intervention, and enhance precision in manufacturing processes.
- Gas and Chemical Sensors:
- Application: Detect the presence of hazardous gases and chemicals in the environment.
- Impact: Prevent toxic exposures, ensure compliance with safety regulations, and protect worker health.
- Vibration Sensors:
- Application: Monitor machinery vibrations to detect abnormalities that may indicate wear or failure.
- Impact: Enable predictive maintenance, reduce downtime, and extend machinery lifespan.
- Pressure Sensors:
- Application: Measure and monitor pressure levels in various industrial processes, including hydraulic and pneumatic systems.
- Impact: Ensure system integrity, prevent leaks, and optimize process performance.
Enhancing Industrial Safety
- Real-Time Monitoring:
- Sensors provide continuous real-time data, allowing for immediate detection of hazardous conditions such as gas leaks, temperature spikes, or abnormal vibrations.
- Automated alerts and shutdown systems can be triggered to prevent accidents and injuries.
- Predictive Maintenance:
- By monitoring equipment conditions, sensors enable predictive maintenance strategies. This approach anticipates failures before they occur, reducing the risk of accidents caused by equipment malfunction.
- Maintenance can be scheduled during non-peak hours, minimizing disruption and ensuring a safer working environment.
- Worker Safety:
- Wearable sensors can monitor workers’ vital signs and environmental conditions, providing early warnings of dangerous exposures or health issues.
- Proximity sensors in collaborative robots (cobots) enhance human-robot interaction safety by preventing collisions.
Boosting Industrial Efficiency
- Process Optimization:
- Sensors collect data that can be analyzed to optimize production processes, reducing waste and improving resource utilization.
- Temperature, pressure, and flow sensors help maintain optimal conditions, ensuring consistent product quality and reducing rework.
- Energy Management:
- Monitoring energy consumption through sensors identifies inefficiencies and areas for improvement, leading to significant energy savings.
- Automated systems can adjust lighting, heating, and machinery operation based on real-time data, further enhancing efficiency.
- Inventory and Supply Chain Management:
- RFID and IoT sensors track inventory levels and movement throughout the supply chain, providing real-time visibility.
- This enables just-in-time inventory management, reducing storage costs and minimizing the risk of stockouts or overstocking.
Conclusion
The integration of sensors in industrial settings is transforming safety and efficiency. These devices provide critical data that enable real-time monitoring, predictive maintenance, and process optimization. By enhancing the safety of workers and the efficiency of operations, sensors play an indispensable role in modern industry, driving both productivity and sustainability.